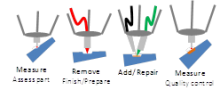
Modern manufacturing is seeing migration of mass production out of traditional European strongholds to low cost economies. However, UK manufacturing industry can continue to be globally competitive by focusing on manufacture of high value customised parts providing significant added value. In order to maintain an advantage in this field there is an urgent need to develop processes which underpin manufacture of such specialised parts. Freeform fabrication is one of the most flexible manufacturing platforms and enables a highly flexible design and manufacturing process, removing many limits of traditional manufacturability, and providing a fluid evolution from concept to product. Additionally, it readily enables difficult but important geometries and uniquely allows for tailored or graded material properties. This project will develop a novel 3D freeform fabrication laser based manufacturing platform. The philosophy behind this is to provide a flexible platform combining the ability to construct, build and add material to freeform shapes with metrology of the created part and the ability to remove material to achieve a high level of form fit and low tolerances in excess of that achievable in freeform manufacture on its own. By integrating fibre delivered laser sources into a parallel robot device we will produce a flexible system capable of a number of concurrent engineering processes. This combines new product development and/or fabrication steps for novel customised parts (such as medical prostheses) or repair of damaged high value components (such as turbine blades) with the ability to monitor the process and measure the component.
Contact Details:
For more information please contact Dr Jon Shephard, J.D.Shephard@hw.ac.uk