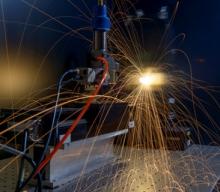
Laser processing is currently highly dependent on user knowledge and experience to choose correct or optimum parameters to obtain a reliable high quality process. Alternatively for every new application or different laser system expensive process development is required. This is the so-called ‘black art’ of laser processing. Furthermore continuous human monitoring is often required to ensure smooth defect free production. The combination of these two factors is greatly limiting the potential exploitation of laser based production process in industry. To tackle this we are proposing two approaches:
|
The eventual aim is to integrate the ELS with the BRL laser process monitoring/control system. When a variation of the welding process is detected, the ELS will automatically correct the parameters accordingly.
Contact Details:
Please contact Professor Stewart Williams for more information, s.williams@cranfield.ac.uk.